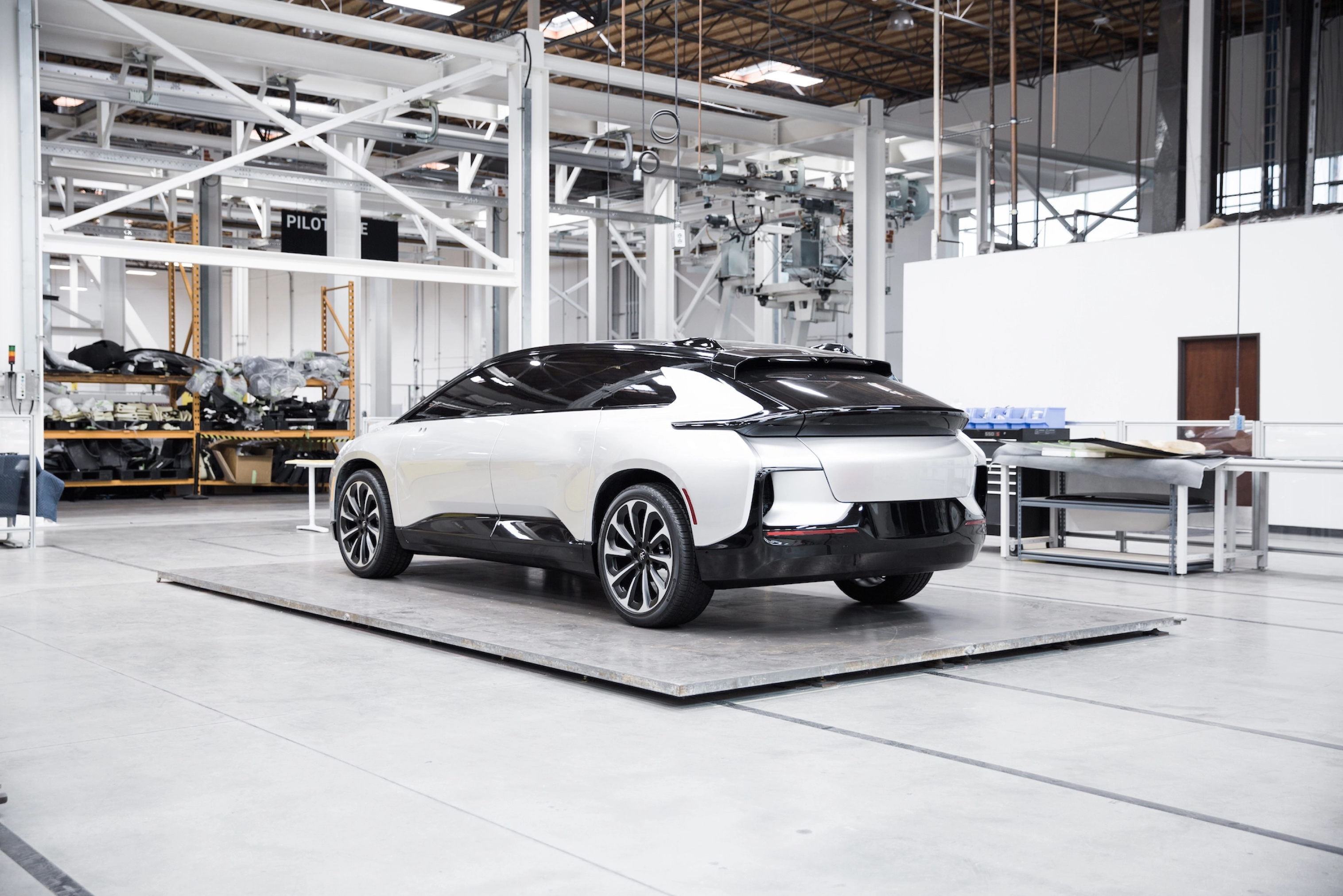
We Created A Fast Paint Masking Solution For An EV Company
- Brand
- Electric Vehicle Manufacturer
- Concept
An EV manufacturer needed a fast, automated way to mask on their paint assembly line as the car was moving. The vehicle being painted had a two tone pattern with a full, glass roof. This meant masks needed to be precise, robust, and able to fit in tight spaces.
01_Challenge
The masking process couldn’t take more than 5 minutes, had to withstand high temperatures, have extra measures for paint leakage, and cleanly remove after the bake cycle.
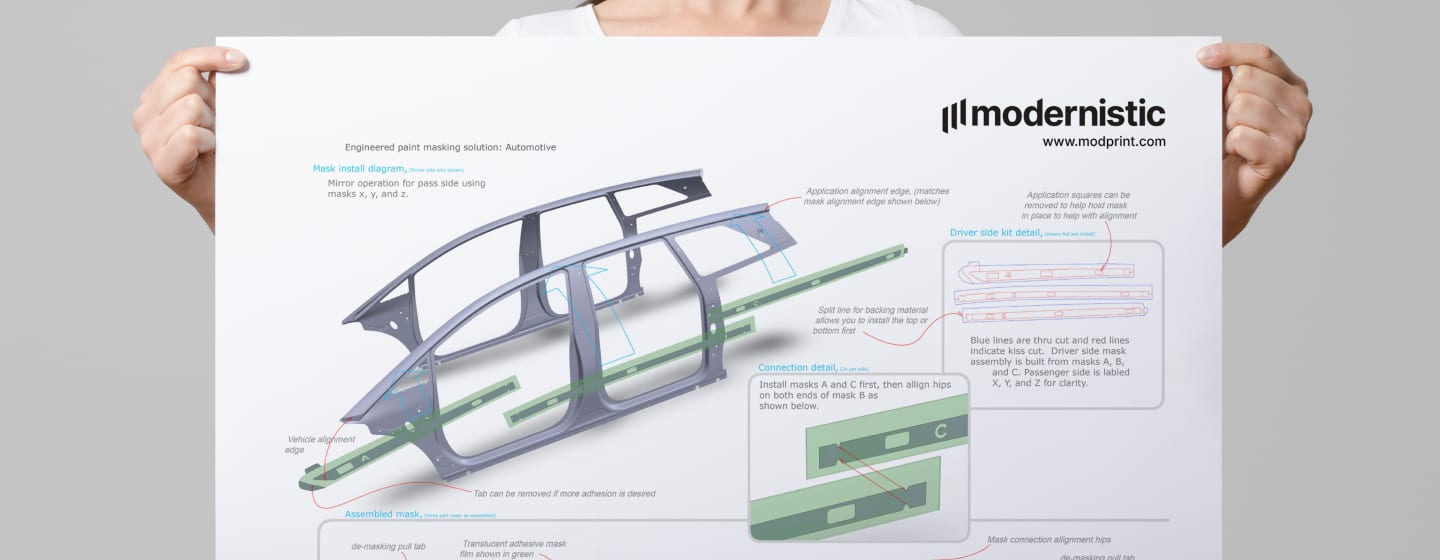
02_Solution
We designed a high temperature mask and developed a shingle system to eliminate paint leaks. The final product was a 3-part mask system involving a center roof panel, windshield panel and rear panel. Our innovative masking design allowed vehicles to be prepped, masked and ready for paint within minutes.
The entire mask system could be applied by assembly line workers in under three minutes, providing the comprehensive paint consistency required to match their luxury brand. This reduction of time and material waste, and increase in overall paint quality has enhanced our customer’s bottom line.