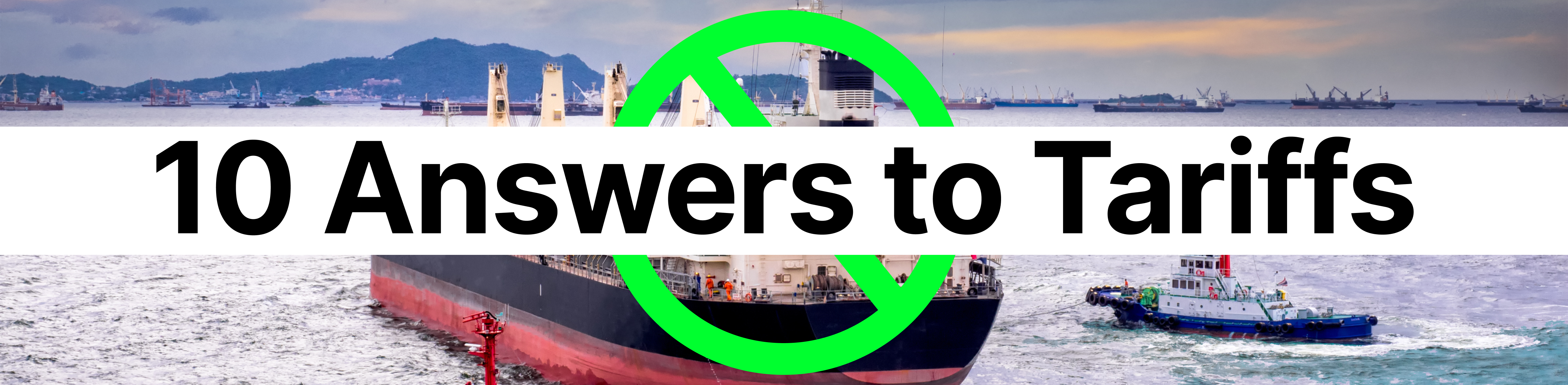
When it comes to custom printing, cutting, and converting, businesses have long faced challenges like rising material costs and supply chain disruptions. Add tariffs on imported goods to the mix, and the cost of doing business with overseas vendors only gets steeper. We’ve been helping our customers sidestep these issues from the start.
Our U.S.-based, all-in-one production model has always eliminated the need for offshore sourcing—no import delays, no surprise fees, no faulty products, and no tariff-related price spikes.
Tariffs may be a newer concern, but the solution isn’t. Delivering tariff-free, hassle-free production for years is just one more reason to move your projects to a smarter, more dependable partner. Let’s dive into our 10 solutions!
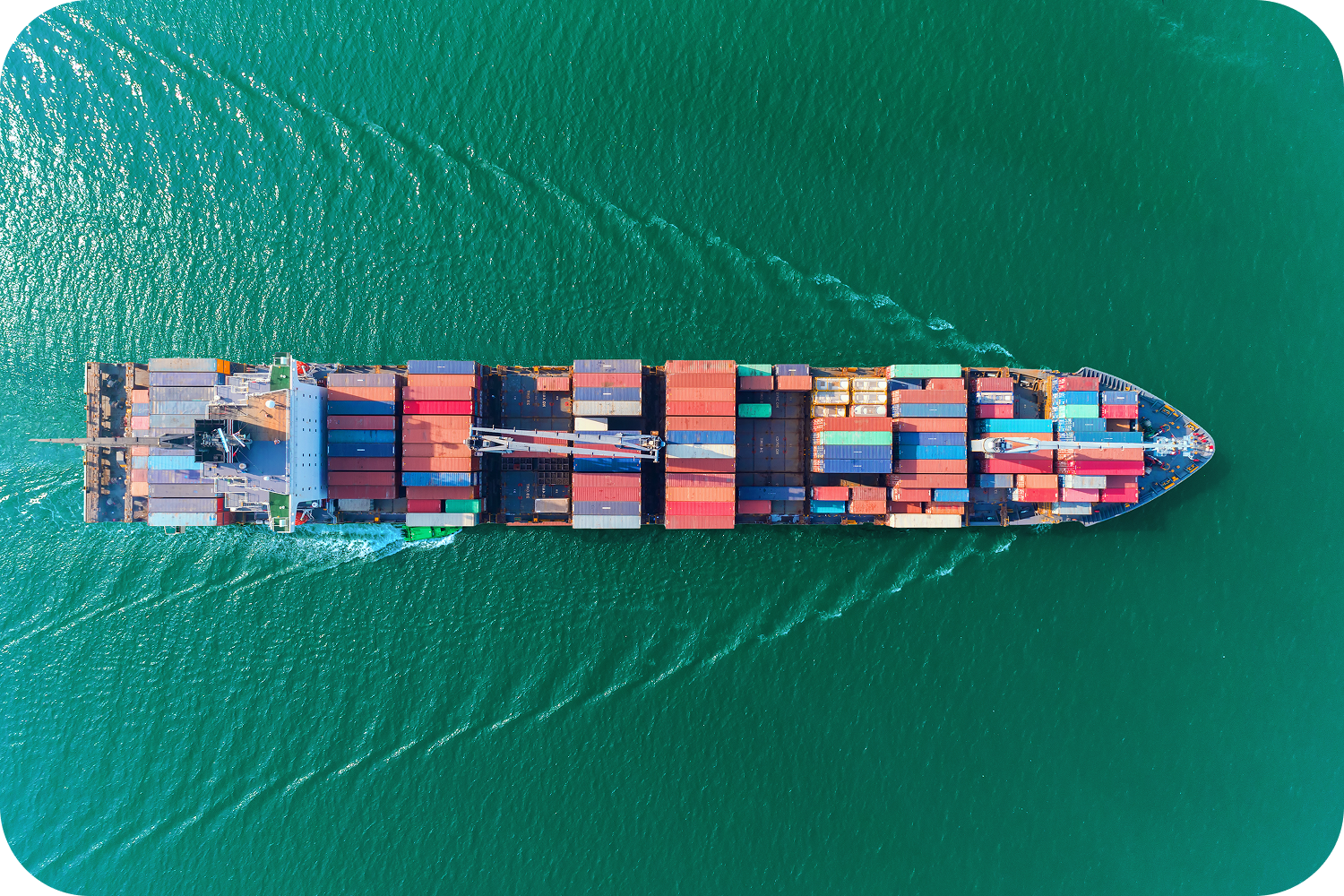
1. Sourcing Materials!
Every day, new materials are being introduced to the market, offering fresh possibilities and innovations for your projects. With over 300 years of combined experience, our estimating team and project managers work closely with a large variety U.S. materials vendors to help you avoid the burden of tariffs and sourcing. We also give customers the flexibility to supply their own materials, ensuring high-quality, on-time production without unexpected import fees or delays.
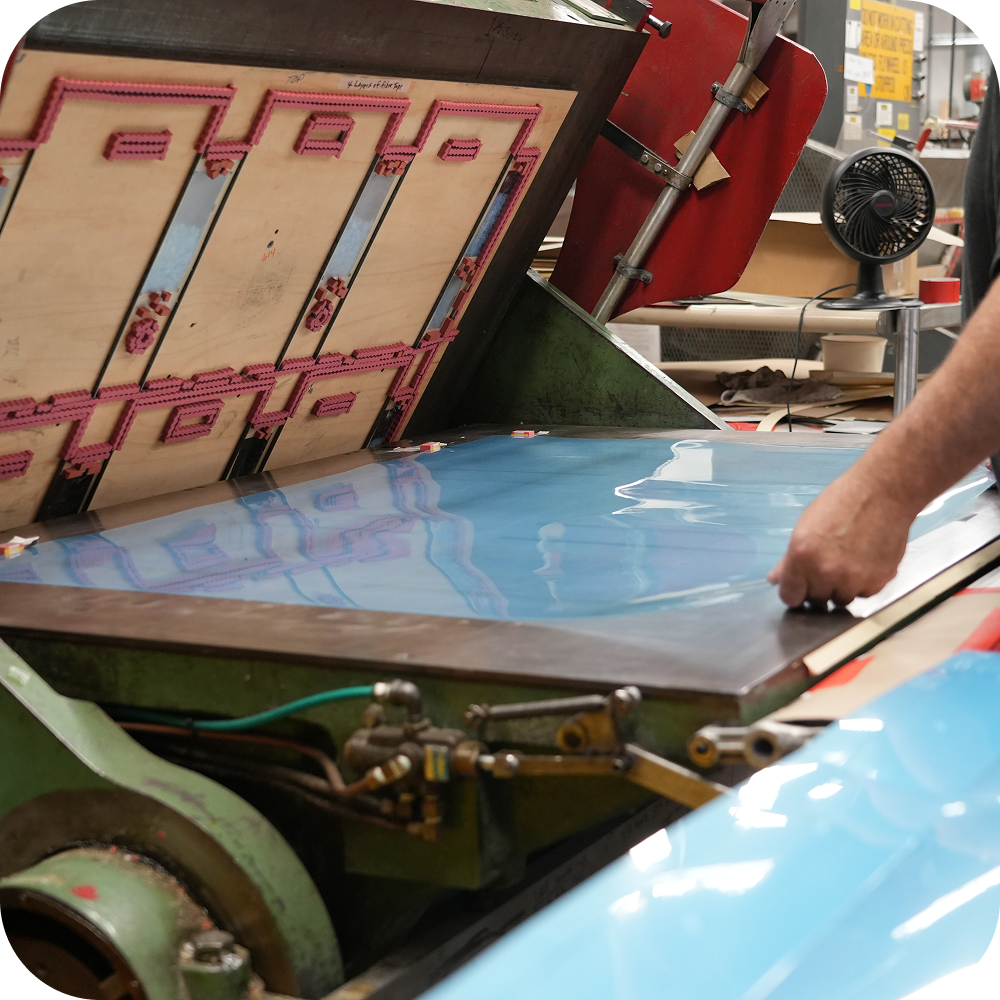
2. All-In-One U.S. Manufacturing
Plain and simple, we give you the most options, centralized in the United States. With all the tools needed to finish a job in-house and vertically overlapped, we can solve any problem, give you exact quality, reduce cost, ship your project quickly, and give you peace of mind with warranties such as the 3M™ MCS™ Warranty.
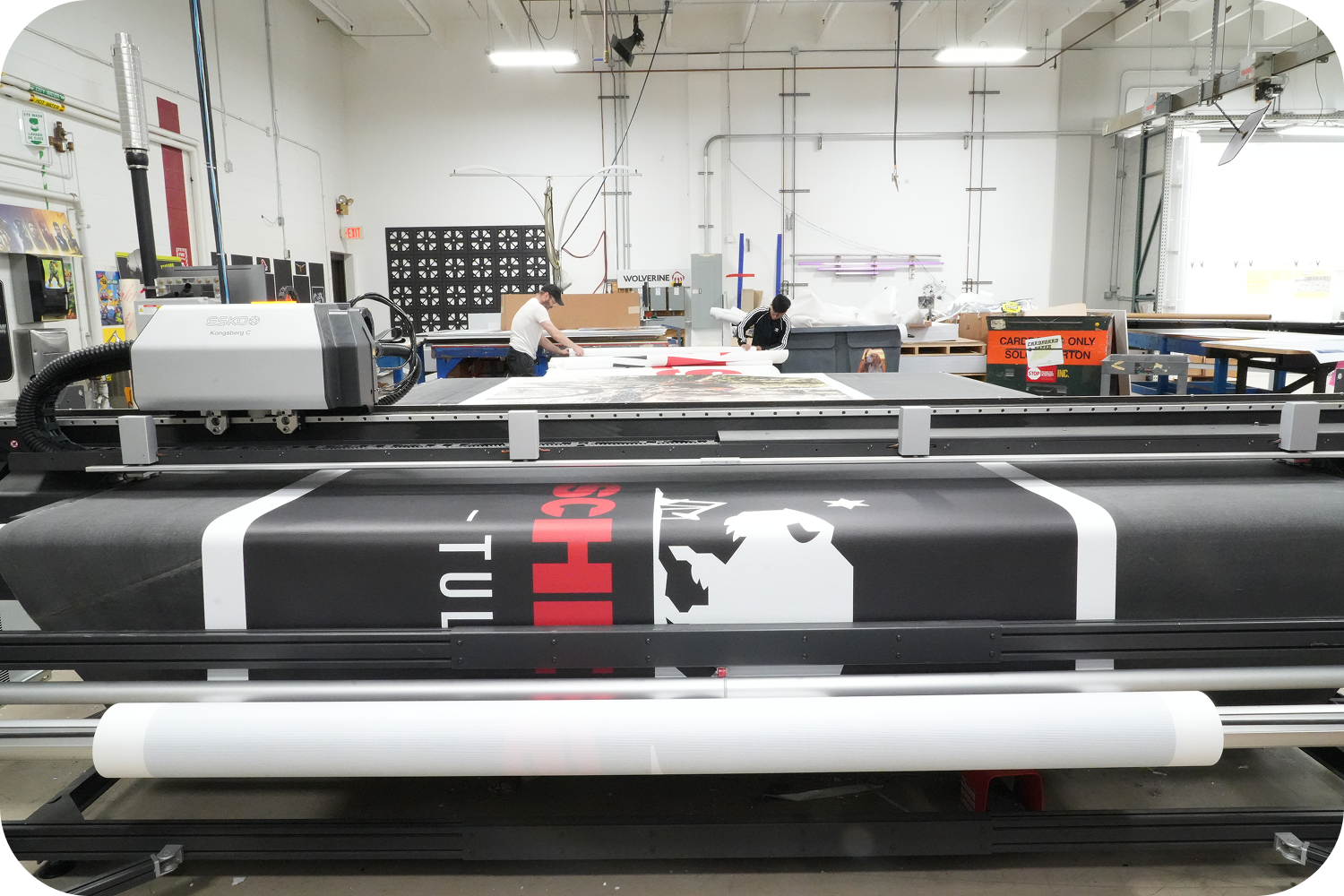
3. Digital & Screen Printing Options
As one of the few printers in the US with both digital printing and screen printing we can quote and offer the best of both worlds — flexibility, quantity, function, quality, color accuracy, and cost-efficiency. By having both options, you don’t have to compromise on your needs or your MOQ (Minimum Order Quantity). We can even interchange processes within that project (screen print + digital printing)! For instance, we can start with digital printing, and if you need a color that falls outside the CMYK gamut, we can add it through screen printing to match it precisely. Do you have a special effect, specialty coating, or an industrial ink – we can do that too!
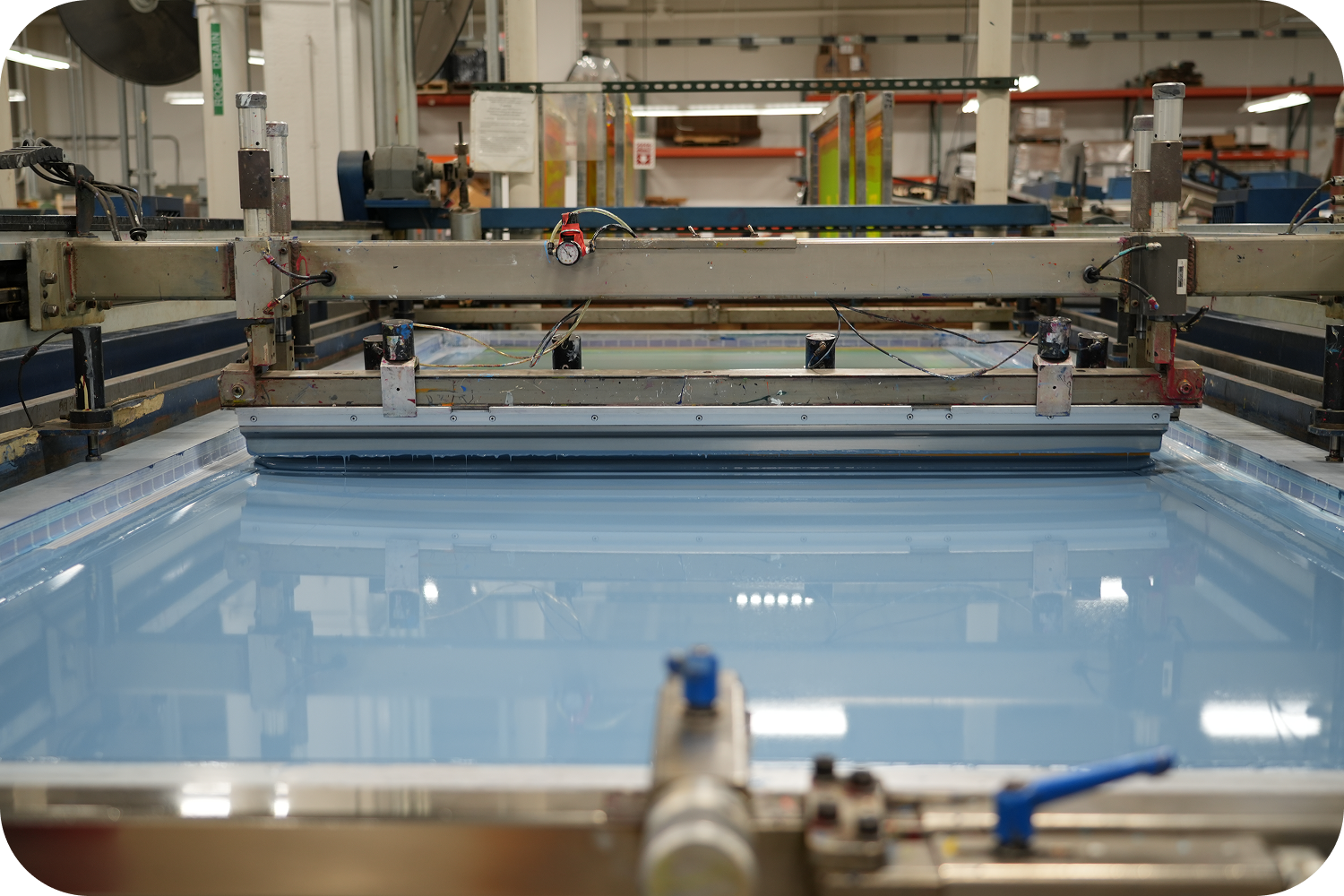
4. Die-cutting & Digital Cutting (Router/ Plotter Cutting) Options
Similar to the value of having both digital printing and screen printing, having die-cutting and digital cutting capability is also rare and invaluable. Other printers have to outsource, transporting product back and forth, which reduces turn around and increases cost. We can cut and fabricate every material with one form of cutting, so you don’t have to bear the additional overhead.
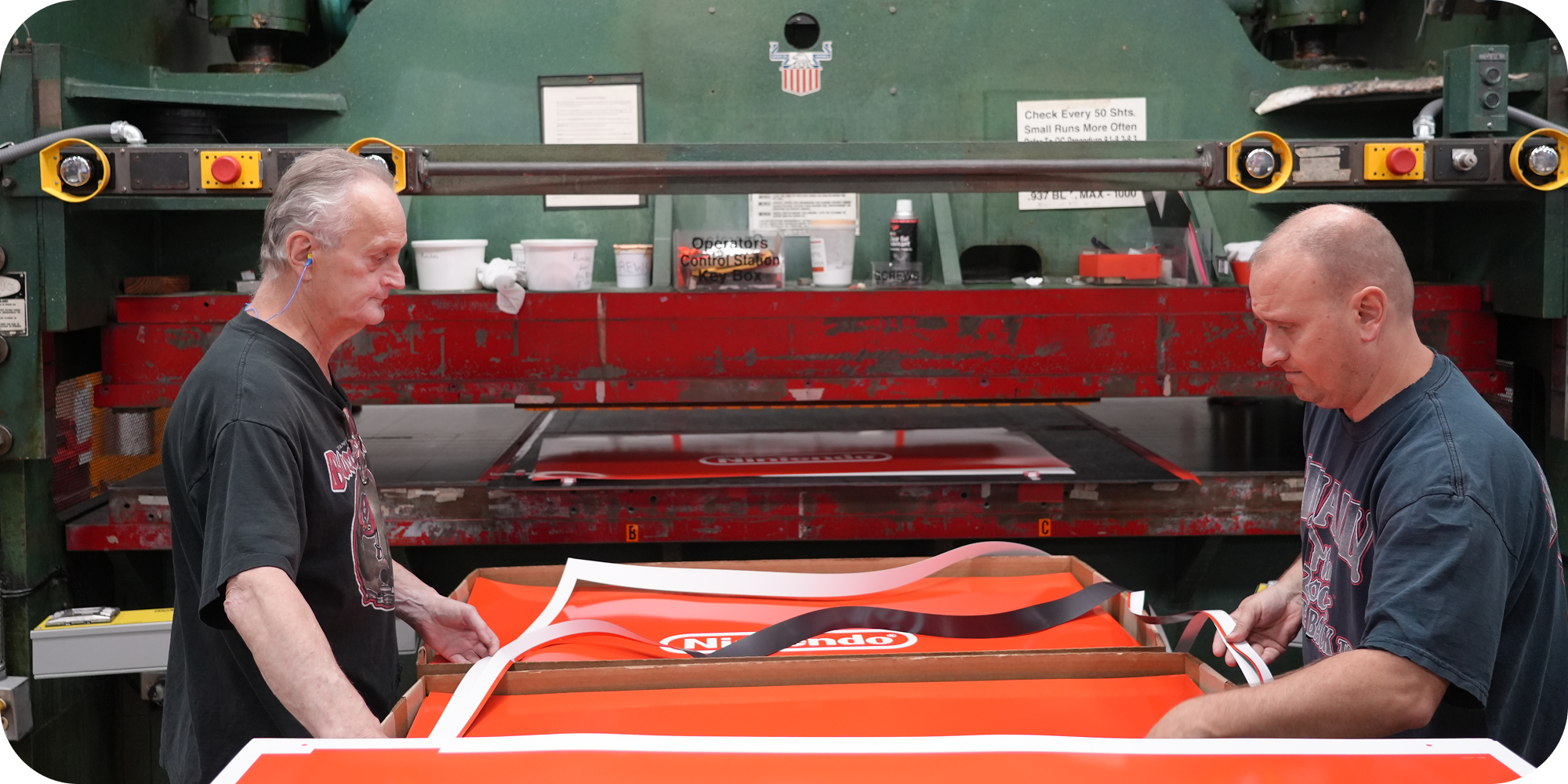
5. Boast Sustainability!
Environmental responsibility has been the fabric of our business model since 2009. Since then, we have reduced our (and our customers’) solvent, material, energy, water, and even gas emissions. We even offer a sustainable material alternative with each project. When you partner with us, you join our movement for a cleaner Earth.
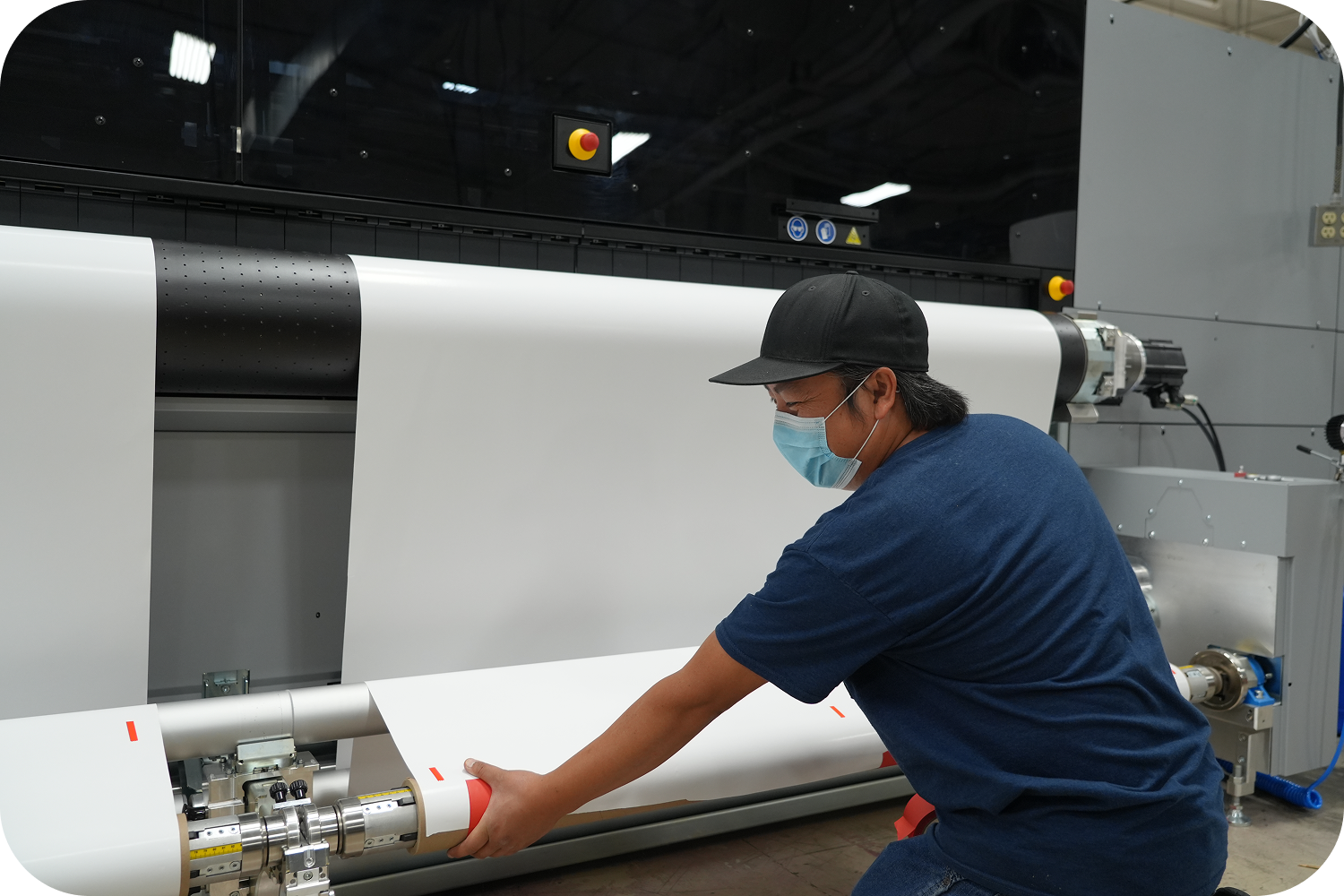
6. Alternate Materials & Material Diversity
As we mentioned, new materials are coming to market every single day. Have a carbon neutrality initiative, need a material that ships lighter, or maybe you just want a substrate that reduces cost? We filter through the noise and curate the best materials for your project. We even have a carbon-negative substrate option!
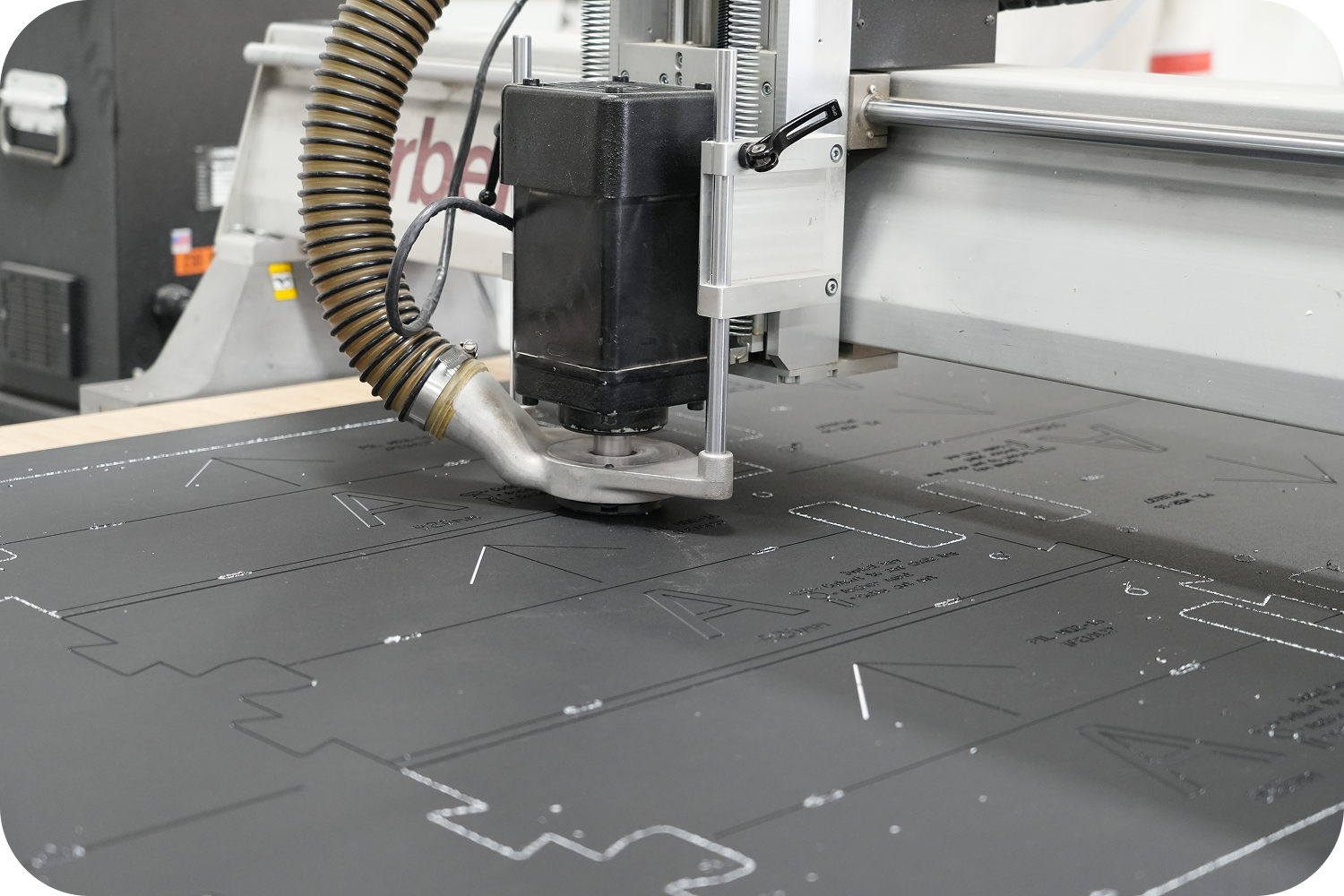
7. Easy Communication (Personal Assigned Project Managers)
Ever heard of Minnesota nice? Every customer is assigned their own project management team—including a sales representative and customer service specialist—who closely manage your project in our facility, works with QA engineers, and keeps you in the loop every step of the way. We prioritize clear communication, transparency, and long-term relationships.
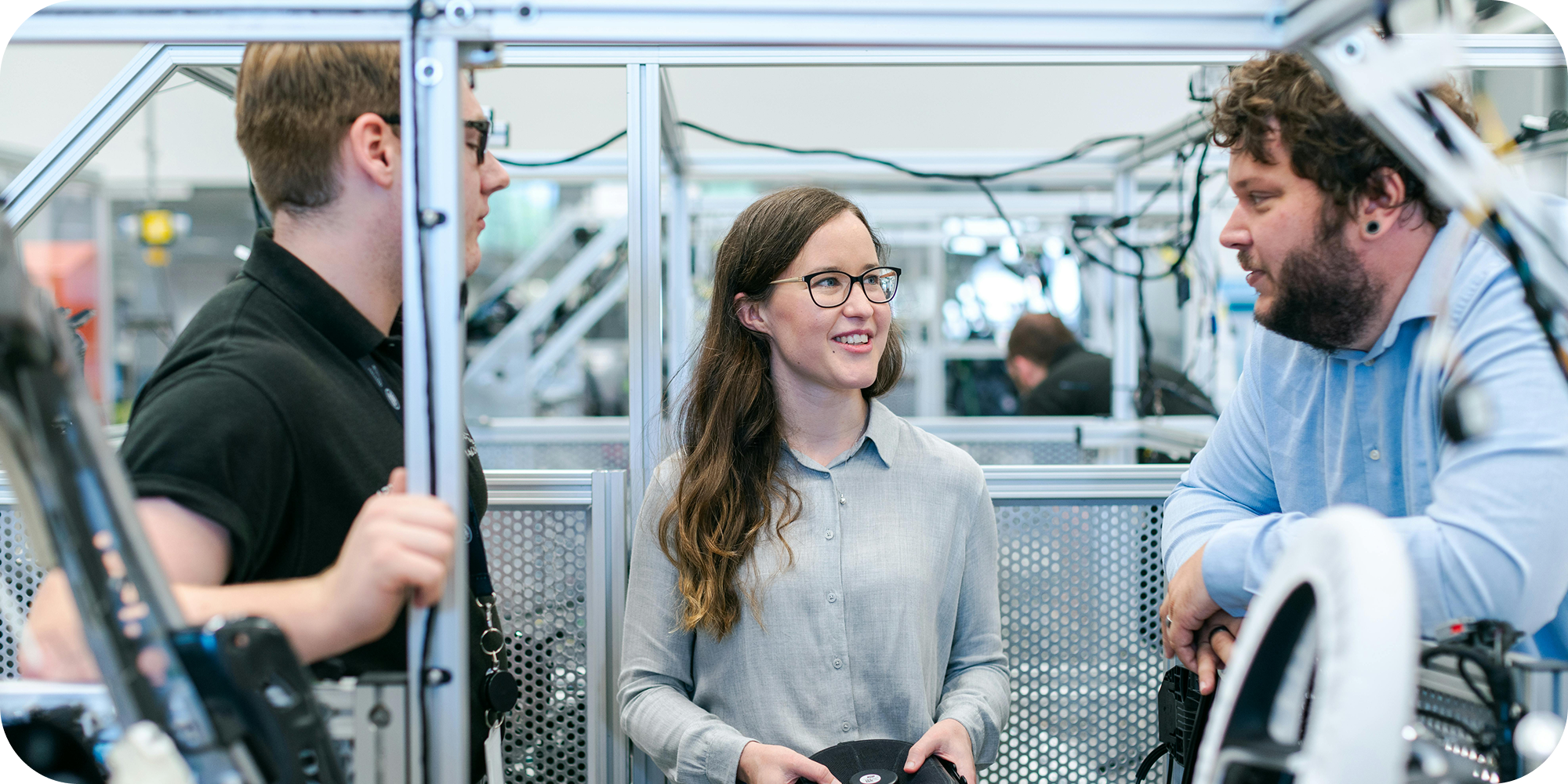
8. Quick Turnaround
Time is money; our overlapping operations will cut down turnaround time and reduce cost. You don’t have to wait for overseas transfers. With very few limitations in our in-house production, our precision and knowledge keep your project momentum going, bringing in your ROI sooner than expected.
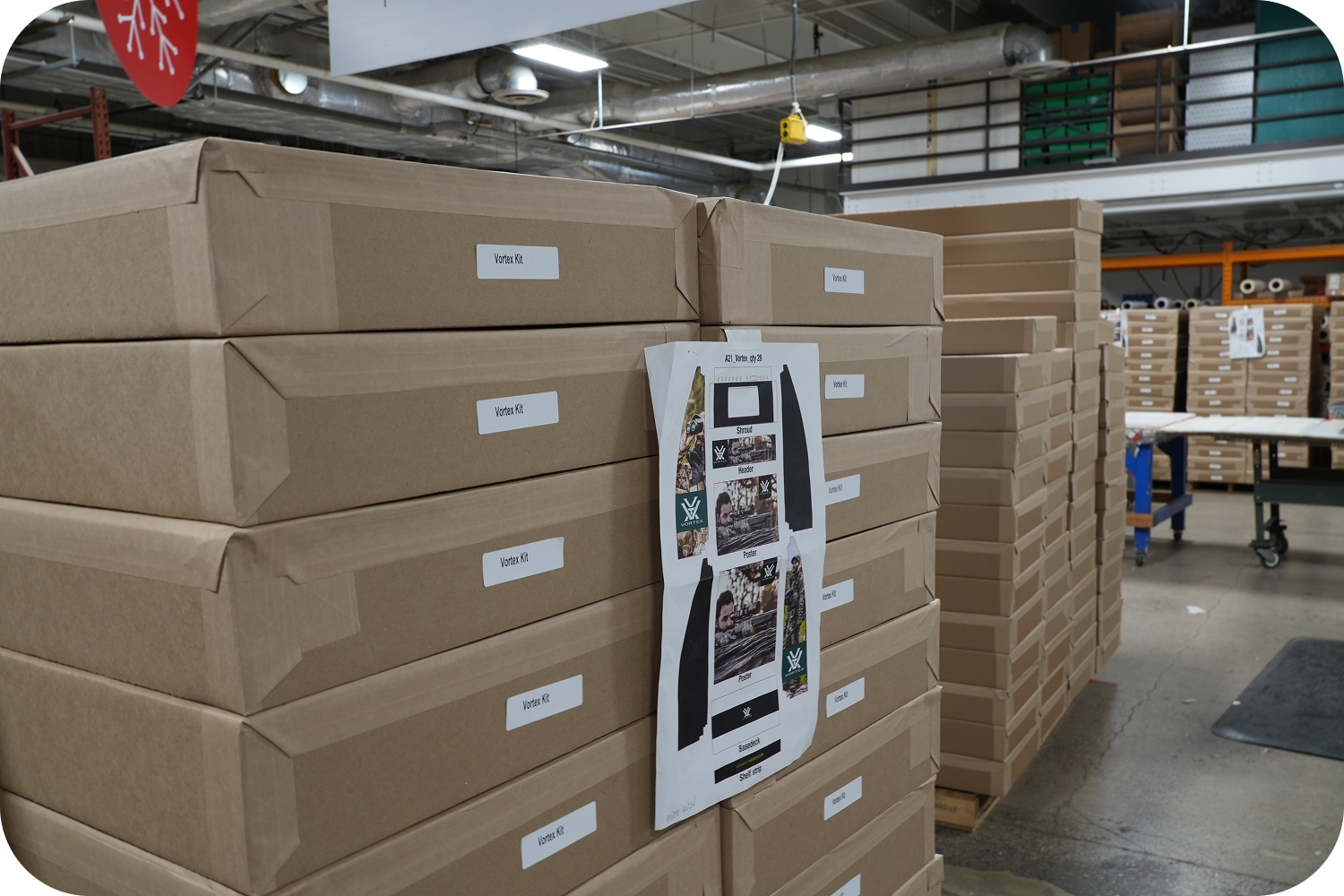
9. Solutions For Every Business Type
We specialize in custom solutions for a diverse range of industries—from aerospace manufacturers to retail brands. Our award-winning Ink Lab formulates unique brand colors that can only be achieved with specialized inks, while our quality assurance engineers measure industrial parts to tolerances that go far beyond the human eye. We’re built for excellence at every step.
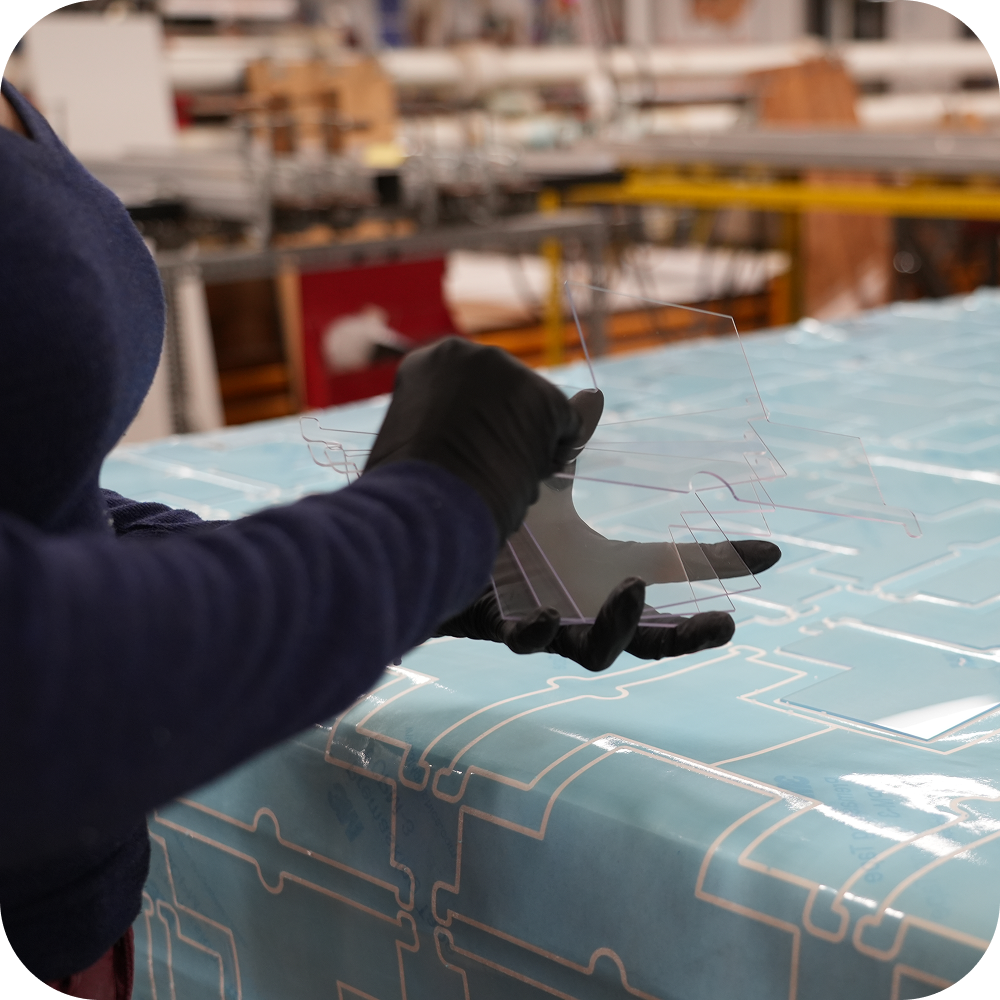
10. Proven Track Record
With over 85 years in the industry, Modernistic has built lasting relationships with clients across various sectors, including retail, transportation, healthcare, and OEMs. Our dedication to quality and customer satisfaction has earned us a reputation as a reliable, tariff-busting manufacturing partner.
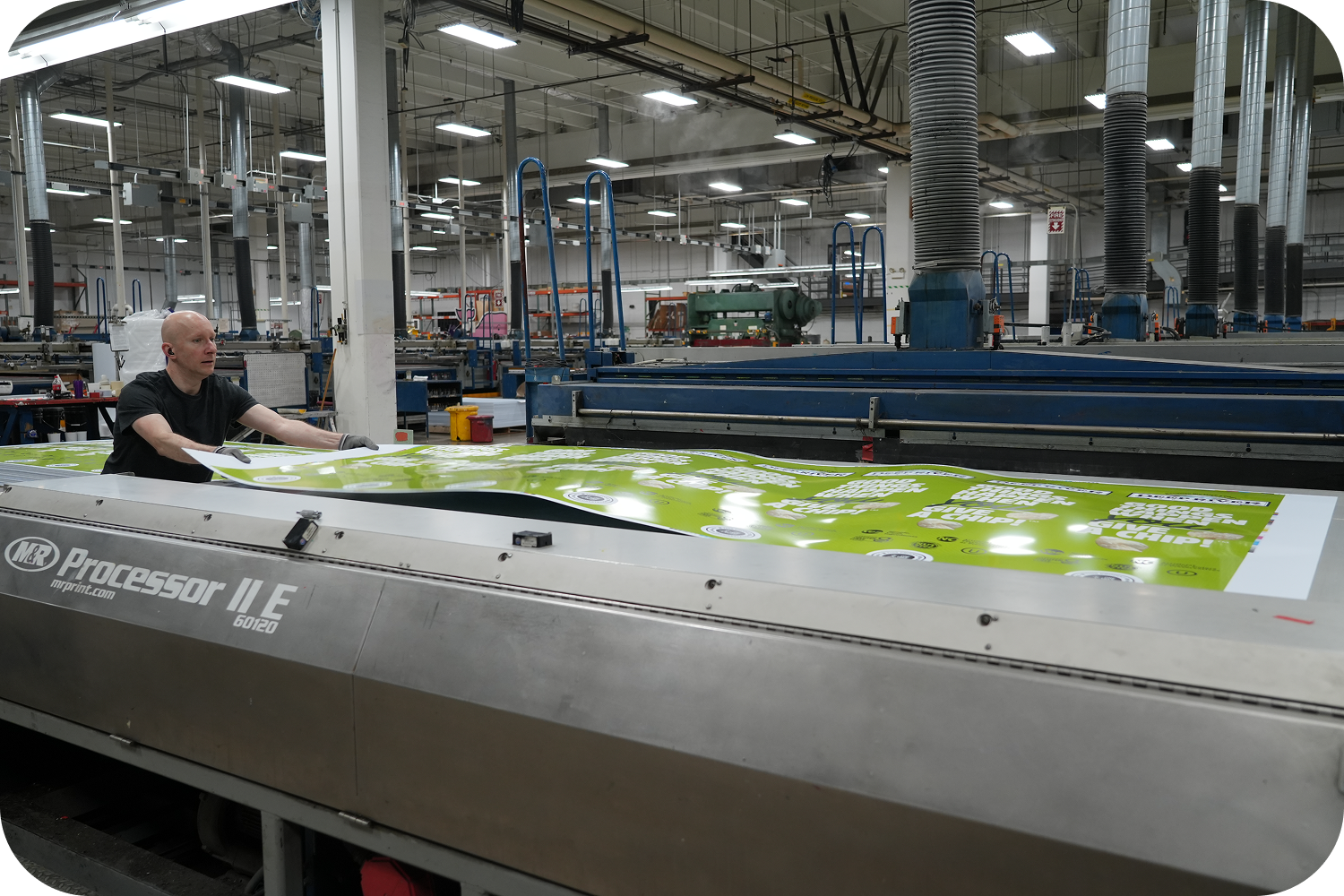
Ready to Go Tariff-Free?
Grow your company’s revenue while looking good to your boss! Breaking free from tariff burdens is awesome, but it takes more than good artwork or a well-structured design to create a great print product. It’s a balanced recipe of great design, affordable manufacturing cost, clever placement, and judicious use of resources. Stay tuned for next month’s knowledge drop to learn more!
On the other hand, if you can’t wait or want to cure your tariff issues RIGHT NOW – click here, and we’ll talk today!